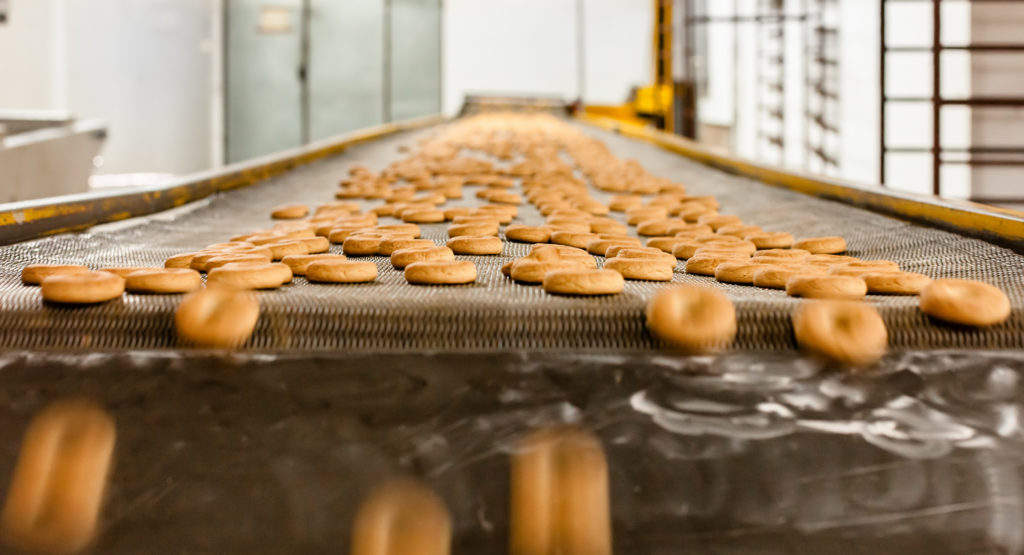
There are considerable advantages to food and beverage companies that invest in technologies that improve operational efficiency, quality and safety. As consumer tastes evolve and competitive forces place additional pressures on companies to reduce costs and deliver more varied products, automation is a critical component of 21st-century food production.
What does it take to implement the right automation tools and processes? Here are five best practices for automating your food manufacturing processes.
1. Evaluate Current Processes
A sound automation strategy begins with conducting a thorough assessment of existing business processes. Review tasks and procedures that are highly labor-intensive, especially those that add little value. The most time and labor-intensive tasks are the top targets for automation.
Look closely too at the way your business management software helps automate processes around finances, production, food safety, compliance, quality, traceability and more. It may be time to reevaluate your current solutions and upgrade to a more robust, food-specific Enterprise Resource Planning (ERP) system.
2. Look for End-to-End Integration
Many manufacturers already have systems that are automated and integrated, operating on a common network or platform. However, full integration is the optimal state, where all systems across an organization are connected and data is shared across the entire business.
Accurate inventory management, for example, is critical for food and beverage manufacturers and can be time-consuming and prone to data error if managed using a separate system, disconnected from the rest of the business. An integrated solution that monitors expiry dates, production volume and inventory valuation helps minimize waste and ensure your entire operation is running as efficiently as possible.
3. Seek Systems with Intuitive Controls
User-friendly automation systems are critical. Without them, there are likely to be higher training costs, especially as food and beverage manufacturing traditionally relies on an older workforce. Automation should use software that is easy to learn, use and master to make adoption as frictionless as possible.
4. Mobility is Key
Today, employees, leaders and key stakeholders can be anywhere, using multiple device types to connect to systems. Increasingly, these devices are mobile. Your automation systems need to support multiple devices and be accessible and functional across platforms. Data needs to be easily accessible from mobile devices and not bind employees to their desks in order to access features.
5. Develop and Track Performance Metrics
It’s important for manufacturers to establish metrics, including key performance indicators, that measure the impact and efficacy of the implemented automation solutions. Whether these measures reflect shortened lead times, less waste, shorter production cycles, fewer processing costs or lower personnel costs, the need for measures against baselines should be determined, tracked and used when automating food manufacturing processes.
These measures can inform not only performance but also other opportunities for improvements and future purchases.
FoodBusiness ERP is a single system to manage your business, including production, operations, finance, food safety, compliance, quality, traceability and more. It works as an automated tracking system for all the moving parts of a business, turning multiple data sets into a single source of information that gives decision makers insight into the business metrics that really matter. If you’re ready to learn more about how FoodBusiness ERP can help you automate your business and processes, reach out to us. We’d love to chat.