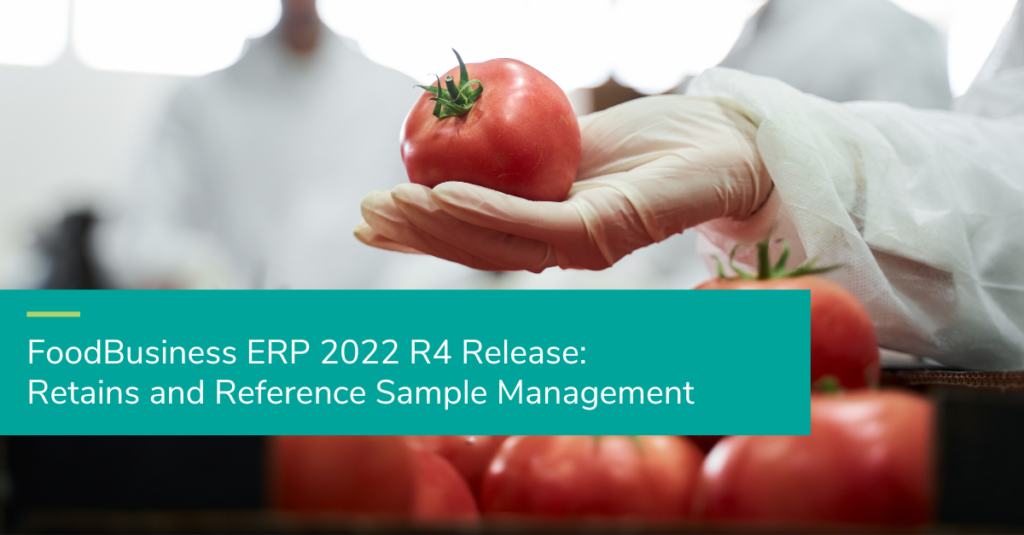
FoodBusiness ERP—built in Sage X3 and delivered by NexTec industry experts—is back office, financials, and enterprise resource planning (ERP) software designed to meet the specific needs of the food and beverage manufacturing industry. Our food software is based on years of food and beverage business experience, and every year, we utilize that experience to provide four product updates—each one building on the improvements and enhancements from the previous release.
Now, we’re excited to introduce FoodBusiness 2022 R4 and its two new features: Retains and Reference Sample Management and Demand Management/Forecasting (check out the details in this recent article). We’ll dive into the first major update today, Retains and Reference Sample Management.
What Retains and Reference Sample Management Is and Why It’s Important
To understand what Retains and Reference Sample Management is, we must first understand that Retain samples are a common requirement in the food industry and many others. Retains can be mandated by a quality standard (e.g., FDA, GMP) or driven by a business’ own quality program.
With this in mind, a retain sample is created by pulling a product sample and setting it aside for future use. Retain samples are quarantined from operational stock and typically moved to a secured storage area. The sample size and retention period may be dictated by compliance or internal quality procedures. Visibility and traceability of retain samples are important and something that many inspectors want to see.
Retains is not the only reason that a company will pull samples. Samples can be pulled from inventory for a variety of reasons. For example, the quality team may run stability tests to determine how a product holds up over time. Test samples can also be used to investigate consumer or internal product complaints, research new products, or track ingredients and compounds.
Retains is a fairly simple concept, but it can be challenging to implement without functionality that is designed to support the process. In fact, if a manufacturer is implementing Retains through configured business processes and not a designed software feature, then the manufacturer’s quality function, stock valuation and employee efficiency may be negatively impacted.
With FoodBusiness ERP 2022 R4 and the quality-focused Retains and Reference Sample Management feature, we’ve mitigated these risks and concerns. Manufacturers can now effortlessly view and manage their sample activity, follow best practices and meet their goal of producing safe and consistent products.
How the Retains and Reference Sample Management Feature Works
Retains and Reference Sample Management is fully integrated with our advanced quality features for management and audit processing. It allows food and beverage manufacturers to save and store samples and enables them to efficiently examine current and past production activity. For example, if a manufacturer wants to perform a stability test—perhaps run it for every two weeks for three months—they can easily do so with this feature, tracking the samples and the data within our food manufacturing software.
There are many benefits of our Retains and Reference Sample Management feature, such as food and beverage manufacturers being able to enjoy both manual and automated audit and test generation capabilities. This integrates sample tests into FoodBusiness ERP’s enhanced quality module and puts the management of the test activity into normal workflows of assignment, response and approval of test results.
Manufacturers will also enjoy:
- Using profiles to group samples together through group assignment functionality (e.g., test samples vs. retain samples).
- Isolating samples via dedicated products, stock status and storage locations to avoid confusion or misuse from active products.
- Converting samples to stock zero value and automatically managing them during sample creation.
- Creating a sample and automatically generating the product, the product site, and the cost, eliminating manual user steps, delays and errors.
- Pulling samples from work in progress to ensure it is within specifications.
- Creating a sample from a sample if a business for specific tests, thereby not tying up the whole sample and using the smaller sample to identify it equally.
- Calculating retention dates automatically but having the capacity to manually edit or adjust the retention date based on information within the sample profile.
- Generating labels upon creation of a sample, or in the case of a reprint or a split off, going back and generating a label on-demand.
Ultimately, our food manufacturing software feature offers manufacturers vital flexibility, especially when dealing with potential product issues or customer complaints. They can not only pull samples quickly and easily, but they will also have the agility to use them when and how they need.
And we’ve established a Sample Workbench, which FoodBusiness ERP manufacturers will use as their “one-stop-shop” for managing all sample activity. The Sample Workbench is where they can view the sample information and make changes, adjust the retain period, manually generate the stock audit or test, and print/reprint labels. It’s also the place where they can go to issue or destroy samples.
Why the Retain and Reference Sample Management Feature Is Both Simple and Powerful
NexTec’s recent guide, “Six Trends Driving Food & Quality in 2022,” notes: “Ensuring food quality and safety is an ongoing, fundamental, and unchanging need.” The guide sheds light on the current safety and quality trends, including what the FDA is doing to improve food safety, how the pandemic has impacted inspections, what role third-party testing plays in quality and safety, what Whole Genome Sequencing (WGS) does, how sustainability is affecting labeling requirements, and more.
More importantly, the guide highlights how food business software, like FoodBusiness ERP, helps food and beverage manufacturers meet—and exceed—safety and quality trends and requirements. And our new Retain and Reference Sample Management feature takes it a step further.
It provides food and beverage businesses with the powerful flexibility and functionality they need to easily and automatically audit and test samples. And it’s simple to set up, simple to manage, and simple to use.
We’ve worked hard to take the complexity and risk out of the process, and we’re excited for FoodBusiness ERP manufacturers to experience the many benefits packed into this comprehensive feature.
If you’re interested in learning more about our new Retain and Reference Sample Management feature and about how FoodBusiness ERP can help your organization ensure unbeatable food manufacturing quality, contact our experts today. We’d love to chat.