Food and beverage manufacturers face unique challenges. That’s why when it comes to choosing the right food and beverage manufacturing software, companies need solutions built with their industry’s needs and requirements in mind.
FoodBusiness ERP helps manufacturers connect their departments, data and processes into a single solution. This gives them the control and visibility they need to take their businesses to the next level.
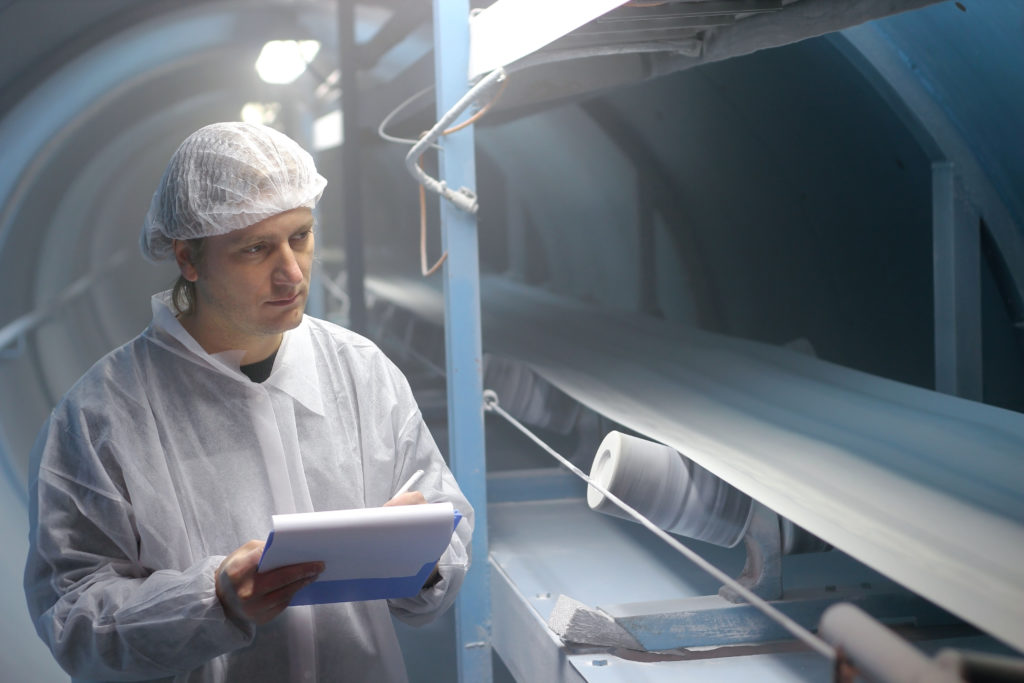
Here’s a closer look into why leading food and beverage manufacturers choose FoodBusiness ERP to run their businesses:
Unique Requirements in Food and Beverage Manufacturing
The food and beverage industry has certain complexities that make an ERP indispensable. The common challenges these companies face include:
- Costing and Margin Pressures – With competition so steep and profit margins razor-thin, companies must be able to improve efficiency in their manufacturing and throughout the supply chain. Without the ability to connect and streamline operations across inventory, sales, procurement and production, inefficiencies can appear and cost a business big money.
- Inventory Management – Accurately managing inventory is a common issue across the industry. By streamlining the way you predict demand, you can reduce food waste, maintain compliance and optimize overall business performance.
- Recipe Control – Your customers expect consistency in the products you create. That’s why recipe management is at the center of a food-specific ERP solution. An ERP for the food industry should include functionality that accounts for different formulations, ingredient and recipe tracking, recipe formulation, allergen management, labeling, ingredient traceability, rework management and track and trace functionality.
- Food Safety – Product safety is high on the priority list of every food and beverage company. To ensure safety and compliance, leading food and beverage manufacturers rely on software that tracks, reports and automates quality processes and traceability measures.
- Changing Consumer Tastes – Change is constant in the food and beverage industry. Consumers today expect access to ingredients, flavor profiles and products from around the world. They want variety in the products they purchase and choice. Tastes – whether fads or the result of changing demographics – can shift quickly. That means companies need the ability to source ingredients and adapt manufacturing processes as these consumer changes occur. An ERP helps manufacturers ensure flexibility.
- Purchasing and Sales – To stay competitive, manufacturers need the ability to manage sales and promotions on a customer-by-customer basis. That requires an ERP solution that can track multiple prices, changing demand, forecasting and accurate order-to-dispatch processes.
These complexities require food and beverage manufacturing software that anticipates industry changes and solves common problems.

Customer Use Case – Increasing Production Capabilities
ARA Food Corp is a 40-year-old family-owned company and the only U.S. manufacturer of the plantain chip. ARA ships its product throughout the country, both under its own brand and private labeled for other companies.
Prior to implementing FoodBusiness ERP, ARA was manually entering manufacturing and accounting information after-the-fact, which led to data accuracy errors. Since going live on FoodBusiness ERP, ARA has been able to:
- Capture data in real time and link it directly to accounting
- Gain visibility into cost tracking, helping to optimize scheduling and resource allocation
- Improve plant functionality
ARA’s business model is unique in that it is a make-to-order manufacturer. “We maintain very little stock, as our ingredients come in fresh every day,” says Marta De Varona, VP of Administration and Finance. “Our lead time from order to shipment is just a few days. We claim that we have the least number of days from production to store delivery in the market. The capabilities of [FoodBusiness ERP built on] Sage X3 helps us achieve that speed and level of agility.”
The team at ARA also uses FoodBusiness ERP’s Business Intelligence (BI) capabilities to help ensure they have a clear understanding of seasonal trends and seasonal production variations in its products. With that data, they can produce production planning reports to ensure they’re optimizing all of their resources.
Features in Food and Beverage Manufacturing Software
FoodBusiness ERP is built on the powerful Sage X3 platform and offers out-of-the-box functionality built for food and beverage manufacturers. This functionality includes:
- Financial Management for real-time visibility into budgets and accounting (general ledger, accounts payable, accounts receivable), fixed assets and financial reporting. It also includes user-defined dashboards, real-time analytics, alerts and a library with more than 400 standard reports
- Supply Chain Management including purchasing (pricing, discounts, suppliers, product categories, RFPs, open orders), inventory management (product data, units of measure, inventory balances, stock movement, import tracking, quality control and sampling), sales management and customer service features to collaborate, manage and remain compliant with global suppliers
- Production Management to get to market faster with features including project cost breakdown structures, employee assignments, multi-level budget description, financial follow-up, time entry and shop floor controls, including labor time collection and time and attendance clocking
- Quality Control including use-by date management, serial number management, batch and sub-batch number management, stock status management (accepted, rejected, inspected), quality control record management and expiration date management
- Bi-Directional Traceability Management to provide critical information quickly to decision-makers, regulators, government officials, customers, consumers and the public
- Collaboration Tools including document and revision management, tag management, sharing capabilities by user, role or team, synchronization of data in Microsoft Excel exports, chart and data insertion into Microsoft Word and PowerPoint applications
- Integration to Sage Applications including business intelligence analytics and reporting, sales and customer management for collaboration between sales reps and office staff, data analytics to provide a hub for data from all sources and in all formats with built-in models for reporting, and e-commerce to create or customize websites with catalogs, pricing, inventory and transactions
Ready to learn more? Our ERP Selection Guide for Food and Beverage Manufacturers outlines the steps you need to take to ensure you’re selecting the right food and beverage manufacturing software for your business. To speak with our team of industry experts, reach out to us. We’d love to show you what FoodBusiness ERP can do.