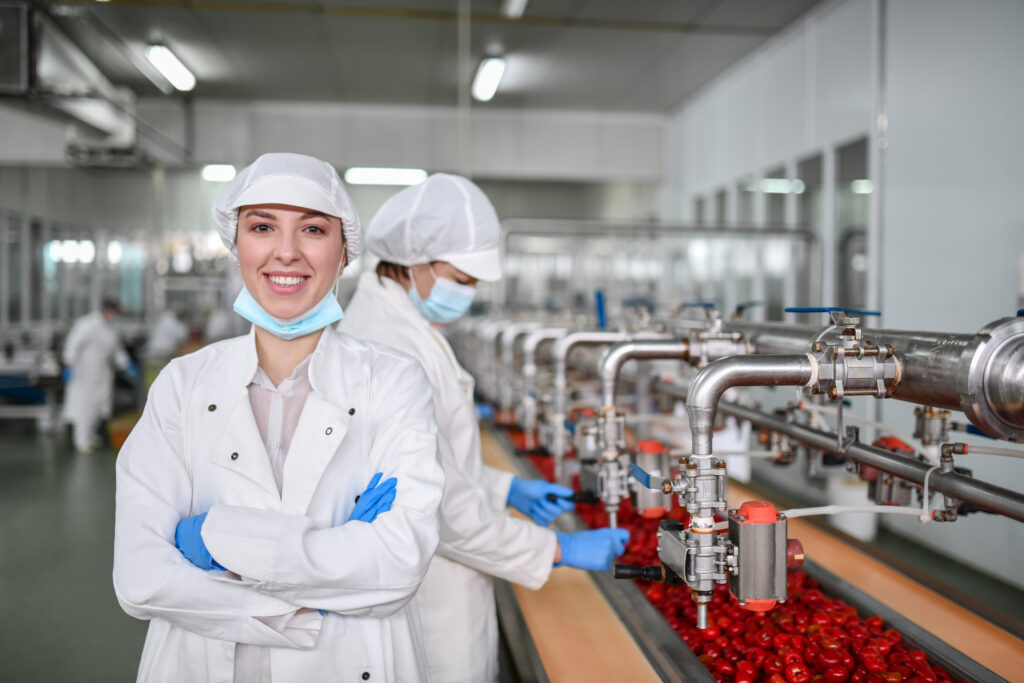
Managing risk in food manufacturing is always a priority, but that is especially true now. Record inflation, supply issues, labor shortages and economic uncertainty are making finding success in food and beverage manufacturing harder than ever.
That’s a lot of change to manage. Disruption is happening in every industry, though, and one of the key takeaways over the past few years has been that information technology is a strategic advantage during times of rapid change. The ability to assess the situation quickly, develop a plan of action and execute rapidly depends on having clear visibility into all aspects of your business and greater control over outcomes.
Got questions? We’ve got answers. Reach out to one of our food industry consultants to learn more about the software.
Let’s look at a few of the risks that food and beverage companies face, and how they can use technology to manage that risk.
How to Manage Risk in Food Manufacturing
Here’s some of the top challenges facing food and beverage manufacturers in 2023 and the role software plays in mitigating these risks:
Changing Consumer Preferences
Changing buyer preferences are a fact of life in the food and beverage industry. Trends towards organic, chemical-free, non-GMO, locally-grown and gluten-free, for example, put pressure on brands to shift operations and adjust ingredients in existing products to offer options that will attract consumers.
This can create real challenges for inventory and production planners. There is a difference, though, between challenging situations and impossible ones. Companies with an established competency around inventory planning and lean production are at a distinct advantage when demand shifts abruptly.
Tools like ERP software built specifically for food and beverage manufacturing comes with features that optimize inventory and production based on real-time company data. Material Requirements Planning (MRP), for example, helps manufacturers:
- Optimize inventory levels to reduce waste.
- Better prioritize production.
- Responsively plan to meet changing customer demands or consumer tastes.
Supply Chain Risks
Although rapidly changing consumer preferences are closely related to supply chain management, they represent only a subset of the broader category of supply chain risks.
Many businesses have chosen to include supply chain disruption in their business interruption insurance coverage. Others have invested in hedging instruments to offset the risk of price fluctuations. There is a third tool available to business leaders to manage supply chain risk, however. Companies with sophisticated production planning capabilities have been better positioned to deal with disruptions, as they are able to reallocate productive capacity to maintain high utilization of people and equipment, even when they are lacking the raw materials to make a particular product.
A recent 2023 report by WTW found that 39% of senior decision makers surveyed believe one of the biggest supply chain factors impacting businesses over the next two years will be a shortage of raw materials.
Companies that are able to optimize inventory levels will ultimately suffer less as a result of the lean management practices they’re able to put in place.
Food Safety, Quality and Regulatory Compliance
The food and beverage industry is understandably subject to close scrutiny by government regulators. Over the past few years, the spotlight was on food safety more than ever before. Tracking the origins of ingredients and raw materials is a standard requirement in the industry, as is the need to demonstrate effective recall processes.
With ERP software designed specifically for the needs of the industry, food and beverage companies can be confident in their abilities to meet an array of ever-changing regulatory requirements. By working with an experienced team of food industry experts who understand that technology thoroughly, food and beverage companies can be confident in their ability to manage product recalls and track products effectively.
Cash Flow Crunch
Like virtually every other industry, the food and beverage sector has suffered from a high level of disruption recently. For many companies, that has resulted in reduced cash flow, or at the very least, cash flow concerns.
The current economy has made liquidity a concern for many businesses right now, and it is possible that many customers will be slower to pay. Disciplined cash flow management is likely to be more common over the next few years as the economy tries to level out.
Once again, ERP technology plays a critical role in managing cash flow expenses carefully. With real-time visibility into customer invoices and collections, the finance and accounting department can exercise a higher degree of control over credit and collections. Real-time visibility to expenditures, likewise, is a key prerequisite to disciplined budget management.
Conclusion
In some respects, the food and beverage industry has experienced greater disruption than many other sectors of the economy over the past few years. Between supply chain issues, food safety concerns and a shaky economy, manufacturers have to deal with huge disruptions. Technology has been a key differentiating factor in helping businesses survive and thrive. Companies that view technology as a strategic asset and invest accordingly achieve agility and resiliency, regardless of what may come in the future.
To see how our food and beverage customers manage risk in food manufacturing and use FoodBusiness ERP to build food better, check out some of our case studies or reach out to us. We’d love to chat.