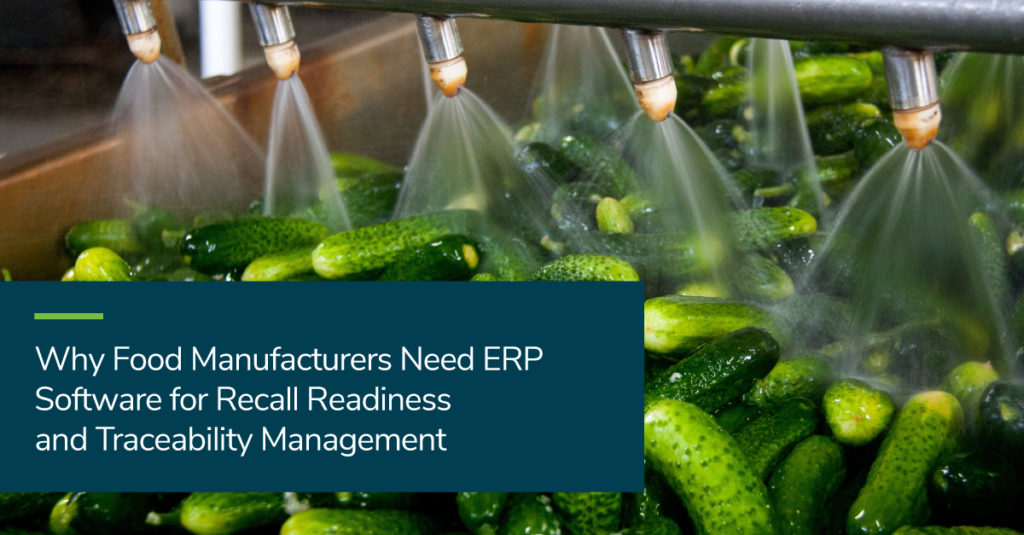
Food manufacturers have a lot on their plate, but when a recall happens, everything comes to a standstill. And it should. Ensuring quality and safety is critical to the wellbeing of their customers and to the success of their operations. According to a Food Safety News article, FDA-regulated firms (food and cosmetic companies) reported 427 recalls for 2021. The article notes that this number is “roughly on par with pre-pandemic years.”
Regardless of how many occur, recalls are inevitable. They happen because of contamination (e.g., listeria or foreign materials), inconsistencies in the product, damaged packaging, unmet product specifications, and more. Obviously, not all recalls are dangerous to the consumer, but they are all dangerous to food manufacturers’ peace of mind, especially those who are unprepared.
How to Prepare for a Recall
Becoming recall ready is a much easier proposition in today’s digital world than it was in the past. Instead of tracking products manually, industry-specific technology, such as food manufacturing software, can help automate the process.
A complimentary eBook offered by FoodBusiness ERP, a food and beverage manufacturing solution built in Sage X3 and delivered by NexTec industry experts, examines how industry-specific ERP solutions can effectively handle recalls. The eBook, Managing Product Recalls in the Food and Beverage Industry, notes, “The way your company responds to a recall can jeopardize your reputation and your profitability. A rapid, efficient and accurate response will help preserve customer confidence and protect your bottom line.”
Preparing for a recall, with or without food business software, should include these basic steps.
- Implement a food safety plan: Though recalls happen, having a food safety plan in place is essential. The understanding and following of regulatory and certification requirements, such as GCFI, FSMA, SQF, GMP, HACCP and HARPC, should be an inherent part of the plan. And the food safety plan should be prepared by team members from different departments, thus bringing a diversity of expertise from across the organization.
- Map out recall procedures: When a recall occurs, even with a food safety plan in place, clear procedures on how the recall should proceed must be made clear to every person in the organization. During this step, determine and designate who will enforce the different procedures.
- Conduct mock recalls: Emergency preparedness training always includes emergency training drills. Do a test run (or runs) with all involved departments, from warehousing, production and transportation to legal and Public Relations.
- Maintain accurate records: Every food manufacturer knows the importance of being able to trace and track production steps, ingredients and products. The same goes with recording ingredient Certificates of Analysis (CoA), process control points, shipping details, vendor information and more. Having this information accessible is just as important as having it in the first place.
Step four brings us full circle back to technology designed specifically to meet food manufacturing production needs. The eBook states, “Industry-specific solutions like FoodBusiness ERP…are helping to drive much-needed change in helping companies prepare for, execute, and recover from product recalls.”
Recall to Fast, Automated Resolution with FoodBusiness ERP
With FoodBusiness ERP, food manufacturers have built-in recall management functionality at their fingertips. A recall loaded into the system triggers the system to automatically generate lists regarding the affected products and quantities, supplier details, shipments involved, and remaining affected stock. The system also flags affected stock as ‘Do Not Use,’ prints required consumer notification letters, creates call lists in CRM to aid customer service reps and assigns and monitors follow-up actions.
Depending on recall type and classification, FoodBusiness ERP also automates the subsequent steps. “If part of your recall strategy to enhance customer experience includes offering rebates, for example, functionality built into a system like FoodBusiness ERP can handle rebate issuing and accounting, helping ensure customer retention and loyalty remains intact.”
Ultimately, the challenges of recall, traceability, and food safety management, such as evolving government regulations, the lack of effective lot tracking, and no system in place, are overcome with modern food manufacturing software and food manufacturing inventory management solutions.
Recall Readiness and Traceability Management with FoodBusiness ERP
When a recall happens (and it will), food manufacturers need to be prepared. FoodBusiness ERP provides the recall readiness and traceability management capabilities they need to effectively address and recover from the ordeal.
Download FoodBusiness ERP’s eBook to learn more about effectively handling recalls, and contact our team today with any questions or to schedule a demonstration. We’d love to chat.