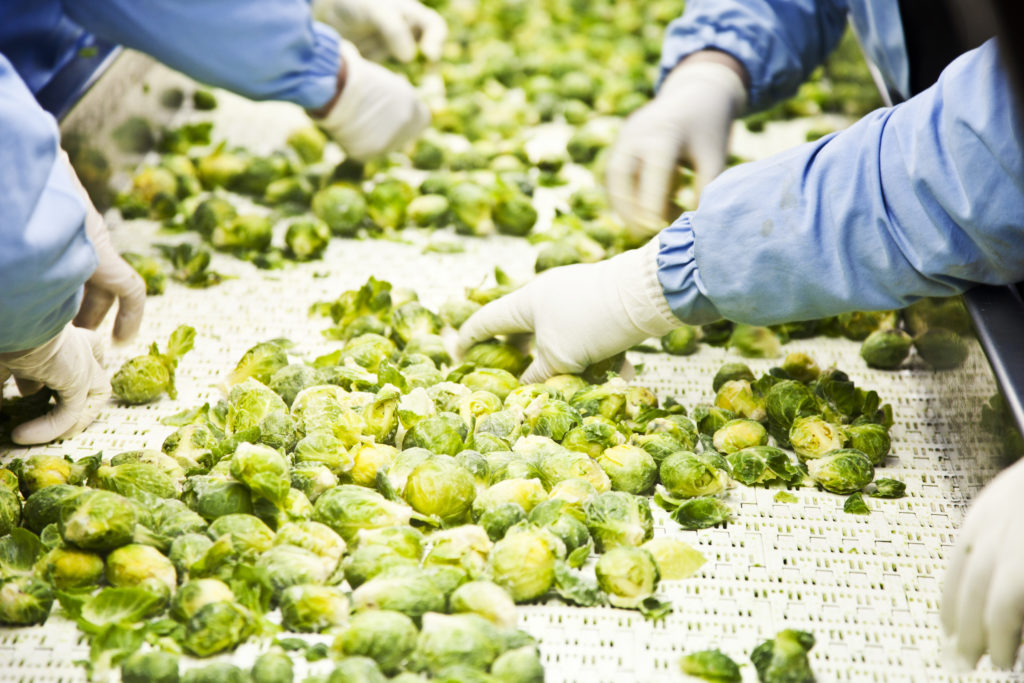
Working with fresh produce is incredibly complex. Growers, processors and retailers are constantly working against the clock to ensure their incredibly perishable products remain fresh by the time they reach consumers. That’s why effective shelf-life management is critical in fruit and vegetable processing.
The Importance of Shelf-Life Management
The shelf life of a product is the period of time before it is considered unsuitable for consumption or sale. During the COVID-19 pandemic, Americans sheltering at home have been prioritizing foods with extended shelf-life, including produce. In April 2020 – a month into the pandemic – purchases of frozen and shelf-stable fruit grew at three to five times the rate of fresh fruit. Though these buying trends have leveled-off over the past nine months, consumers are still looking for healthier items that will last.
Improper shelf-life management can have a big financial impact on a business. Companies that don’t prioritize waste reduction with effective shelf-life management measures risk profitability, customer satisfaction and brand image.
Champions 12.3, a coalition of stakeholders from across the globe who are dedicated to tackling food waste, analyzed 700 manufacturing, retail and service companies and found that half of those that invested in the reduction of food waste saw a return on those investments of at least 14 times what they spent.
The financial impact of reducing waste coupled with a rise in eCommerce and food delivery demand accelerated by the pandemic, is motivating produce processors to consider new technology to streamline their operations and bolster their shelf-life management capabilities.
Extending Shelf Life with ERP for Fruit and Vegetable Processing
Enterprise Resource Planning (ERP) software with food-specific functionality is a critical tool for produce processors. Below, we highlight some of the features in an ERP for fruit and vegetable processing that will help with proper shelf-life management to keep your business profitable and competitive:
- Expiration Date Tracking
With an ERP, processors can allocate inventory to sales orders and production based on the First Expired, First Out (FEFO) method of expiry date management. The concept of FEFO is simple: products with the earliest expiration date are the products that will be used or sold first. This method is especially useful for food companies working with highly perishable goods, like produce.
An ERP system connects manufacturing, ordering and customer data into one solution to help implement FEFO across your operations. Assigning expiration dates to items at receiving and tracking this data throughout the production process will give you the visibility and insight you need to be able to send the oldest allowable stock to each customer with ample shelf life. This helps reduce stock age and results in less stock write offs.
If inventory nears expiry, an ERP can be set up to identify it as suitable for promotion or discounts to help move inventory quickly. An ERP also works behind the scenes to consider the length of each product’s life cycle to help better plan reordering processes and reduce inventory waste.
- Finished Stock Management
An ERP solution with industry-specific functionality enables processors to monitor the shelf life of finished goods across multiple storage facilities. Users can create rules for handling specific items, such as guaranteed shelf-life minimums. When a customer with specific shelf-life requirements has a product being allocated to its sales order, the system makes sure the guaranteed shelf-life minimums are being met. These rules make it simple to verify that you are sending the right stock to customers at the right time.
- Quality Control
All ingredients used in food and beverage manufacturing must be carefully monitored and tested from the time they enter your facility until they’re delivered to your customer. With an ERP solution, users can monitor the quality and freshness of an ingredient at each phase using automated quality checks and audits. These audits can be set up to occur during production and again before items are shipped. In each quality audit or test, a range of testing parameters can be accounted for, including weight, viscosity, pH, temperature and other critical factors that will aid in your shelf-life management processes.
- Recall Readiness
Shelf-life management functionality found in an ERP for fruit and vegetable processing greatly decreases the risk of a product recall occurring in your facility. However, if one should occur, an ERP is your best tool in minimizing the impact of a recall on your business. With an ERP solution, information can be easily accessed to identify which items may be at risk and enables you to pause production and place a hold on any affected inventory. An ERP system with built-in traceability functionality also allows you to simplify recall reporting measures and narrow the scope of a recall, saving you time and money.
FoodBusiness ERP is purpose-built for the food and beverage industry and offers out-of-the-box functionality to help manufacturers and processors streamline efficiency and manage growth. To learn how FoodBusiness ERP can help your produce processing company improve its shelf-life management capabilities, reach out to us. We’d love to chat.